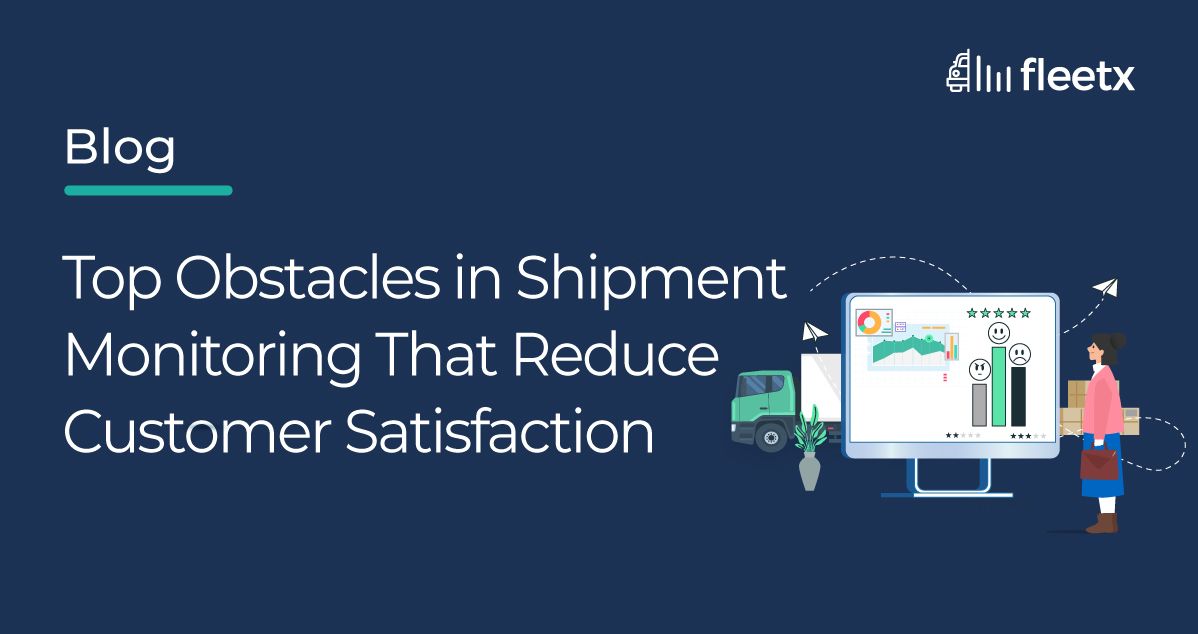
Effective shipment monitoring is one of the key processes to ensure the smooth flow of goods and, ultimately, customer satisfaction. As businesses increasingly turn to smart technology solutions for fleet management, there is now a movement in the industry to further develop innovative technology, and provide solutions to specific logistical challenges.
In this article, we explore commonly experienced challenges that prevent efficient shipment monitoring, how that can impact customer satisfaction, and provide viable solutions to address each challenge.
Obstacles to Effective Shipment Monitoring
Lack of Real-Time Visibility:
One of the major obstacles to shipment monitoring is the lack of real-time visibility. In an era where on-time delivery is key variable in measuring satisfaction, delays in tracking the exact location and status of shipments can lead to customer dissatisfaction. Businesses need a solution that provides instantaneous updates and allows them to stay ahead of potential disruptions.
The Solution: Enhanced Visibility
To overcome the challenge of limited real-time visibility, businesses should invest in smart technology solutions that offer real-time tracking capabilities. GPS-enabled devices and advanced tracking systems provide up-to-the-minute information on the location, condition, and estimated time of arrival of shipments. This not only enhances customer satisfaction but also allows businesses to make informed decisions in real-time.
Data Integration Challenges:
Shipment monitoring involves compilation and analyis of data from various sources, including GPS devices, sensors, and other tracking tools. The challenge lies in integrating these diverse data streams into existing systems. Companies using older technology can face issues with compatibility and cross-platform operations, limiting their ability to harness the full potential of their fleet management systems.
The Solution: Seamless Data Integration
Addressing data integration challenges requires a comprehensive approach. Implementing a centralized platform that can collect and aggregate data from various sources is an essential step. For example, cloud-based solutions with robust APIs facilitate seamless integration, ensuring that all relevant data is accessible in a unified dashboard. This integrated approach enhances the accuracy and reliability of shipment monitoring.
Limited Data-driven Decision Making:
Anticipating potential issues before they occur is helpful in preventing disruptions to the supply chain. Unfortunately, many companies still struggle with implementing robust predictive analytics. This often results in reactive rather than proactive measures, impacting the overall reliability of shipment monitoring.
The Solution: Predictive Analytics
To move from reactive to proactive shipment monitoring, businesses should leverage predictive analytics. Machine learning algorithms can analyze historical data, identify patterns, and predict potential disruptions. This foresight enables companies to take precautionary measures, reducing the likelihood of delays and enhancing overall customer satisfaction.
Communication Gaps and Limited Collaboration:
Effective communication and collaboration among stakeholders are critical to ensuring the smooth flow of the supply chain. However, communication gaps between drivers, warehouse teams, and other involved parties can lead to misunderstandings, delays and cascading consequences. Limited collaboration can hinder the quick resolution of issues, impacting customer satisfaction.
The Solution: Enhanced Communication and Collaboration
To address communication gaps and foster collaboration, companies should invest in communication platforms that enable real-time interaction among all stakeholders. Mobile apps, instant messaging, and collaborative tools can bridge the communication divide between drivers, warehouse teams, and other parties involved. It is also worthwhile to invest in a centralized communication hub that ensures everyone is on the same page, reducing the likelihood of misunderstandings and delays.
Inadequate Security Measures:
With the rise of cyber threats, ensuring the security of data related to shipment monitoring is a growing concern. Inadequate security measures can expose sensitive information, leading to data breaches, unauthorized access, and potential disruptions in the supply chain. This not only
poses a threat to the company's operations but also diminishes customer trust in the event of a security breach.
The Solution: Robust Security Measures
In response to the growing digital threat landscape, companies must prioritize cybersecurity in their shipment monitoring systems. This involves implementing robust encryption protocols, regularly updating software and firmware, and conducting thorough cybersecurity training for employees. Investing in a secure infrastructure protects sensitive data from unauthorized access, ensuring the integrity and confidentiality of information throughout the supply chain.
To Wrap Up
Overcoming the obstacles in shipment monitoring is a big step forward for businesses aiming to provide improved customer satisfaction. Investing in smart technology solutions that address real-time visibility, seamless data integration, and predictive analytics is the key to unlocking the full potential of fleet management systems. The ability to anticipate and address potential issues before they impact deliveries fosters trust and confidence, leading to a satisfied client base.
The holistic approach outlined in this article empowers businesses to build resilience in their fleet management systems and deliver a level of service that exceeds normal customer expectations. This helps to foster long-term relationships and solidify your in the competitive logistics industry.