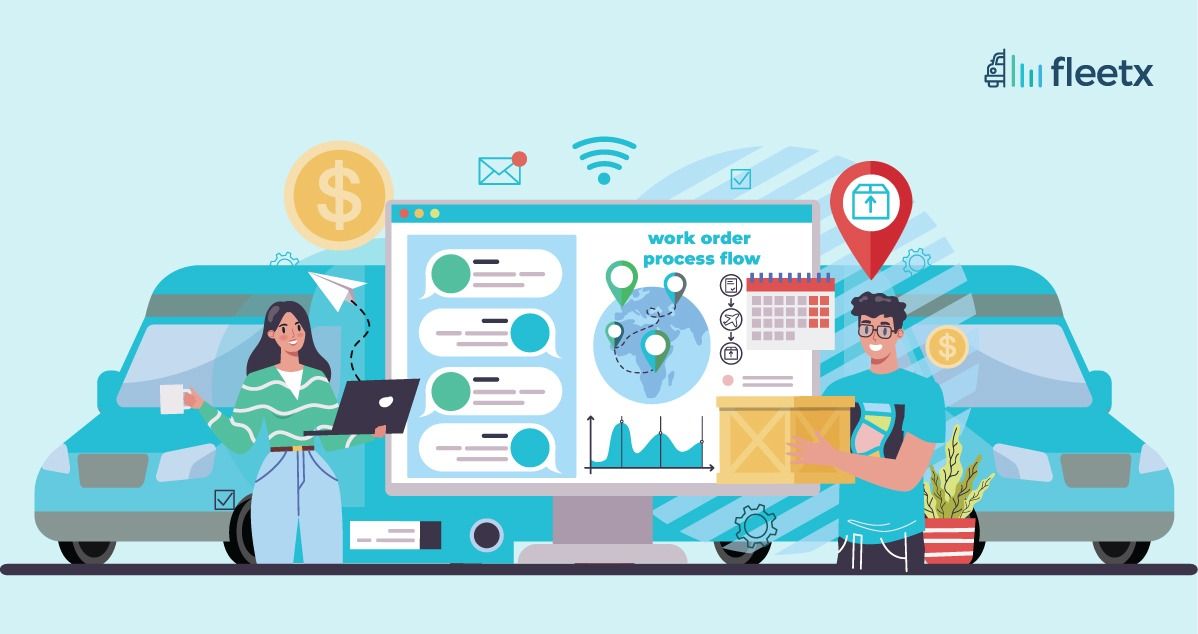
Work orders are an essential component of fleet maintenance because, before establishing fleet maintenance management, fleet managers must regulate workflows. Improving the work order process increases the efficiency of a fleet's maintenance activities; having an optimized work order might be a good option for a business.
Fleet managers fail to pay attention to every tiny yet important activity, such as regular vehicle maintenance and service, and these minor errors can lead to compliance failure, lapses, breakdowns, and unnecessary operational expenses. These obstacles are easily solved by incorporating work order management with a connection to technological automation into the company's existing fleet maintenance processes. As a result, it is critical to recognize that work order management is the bedrock of any good maintenance programme. So, what exactly is a work order?
What is a Work Order?
A work order is a document that contains all of the necessary information concerning a maintenance task. It also describes the steps necessary to finish the work. Work orders may include information about the task's scope, who authorized it, the technician assigned to the job, and the expected results. These instructions are critical for the maintenance of a fleet.
Additionally, work orders assist drivers, technicians, workshop managers and fleet maintenance managers in prioritizing, organizing, assigning, completing, and tracking key jobs. Once completed, work orders help fleet managers capture vital information that is useful to improve efficiencies.
What Exactly Is Work Order Management?
Work order management is the process of ensuring that maintenance activities, inspections, and repairs are completed on schedule.
Operations managers may easily accomplish compliance targets and extend the life of their fleet with an effective work order management procedure. The entire supply chain process is simply made more smoother and more efficient when work orders are managed efficiently. Since, disruptions to productivity are eliminated, vehicle lifespan increases, drivers are better controlled, and overall operations can be performed quickly.
Moreover, work order management effectively arranges the necessary resources and coordinates the related parts and supplies to complete the specified tasks. They involve more than just future planning, though. Work orders aid the maintenance division in tracking previous activities and offer valuable information that may be used to support data-driven decision-making.
Are work orders and preventive maintenance interrelated?
Preventive maintenance is a heavy task and deals with many different fleets and datasets. Analyzing work order history before and after implementing a preventive maintenance programme is critical to understanding the situation and completing tasks on time. There should be some specific work orders done to have an efficient fleet preventive maintenance program, and that includes a digital platform to schedule route maintenance with reminders and service requests, a digital inspection checklist, vehicle fault alerts, jobs, and a maintenance checklist.
What are the types of work orders?
There are six types of work orders. Below are the details of each type of work order.
General: Maintenance operations that do not fit within the categories of preventive maintenance, inspection, emergency, or corrective maintenance work orders are included in a general work order. General work orders may involve duties such as installing new equipment, removing obsolete equipment, or painting.
Preventive maintenance: Preventive maintenance work orders are routine tasks performed on assets to avoid costly equipment breakdown and unplanned machine downtime. For each activity, this work order includes resource requirements, instructions, checklists, and notes. They are also put on a schedule to guarantee that the maintenance activity is completed at a regular period.
Inspection: When a maintenance technician has to audit or examine the state of an asset, an inspection work order is issued. This is frequently based on a time frame, comparable to preventive maintenance work orders. A maintenance professional may find a problem during an inspection and then create a new work order to address that problem.
Emergency / On-demand : When an unanticipated asset breakdown happens and needs to be fixed immediately away, an emergency work order is prepared. An emergency work order documents and tracks reactive maintenance.
Corrective maintenance : When a maintenance technician detects a fault while performing preventive maintenance, inspection, general, or emergency work order chores, he or she creates a corrective maintenance work order. A corrective maintenance work order, as opposed to an emergency work order, is planned and scheduled because the issue was discovered in good time. A corrective maintenance work order could include repairing, restoring, or replacing equipment or parts.
Third-party : The majority of work orders for most maintenance are internal. However, some functions are performed outside, which falls under the purview of a third party. In businesses, there is work that must be done that is beyond the technical capabilities of the maintenance team, and this work is outsourced and completed by third parties.
What is work order process flow?
Every maintenance work order has a process that is divided into three parts: creation, completion, and data recording. Task identification, requesting a work order, scheduling the work order, assigning and finishing the work order, documenting and closing the work order, and reviewing the work order to assist improve the process for the next time are some of the processes. The work order process flow consists of six steps, which are as follows:
Task identified: Work orders begin when an issue is discovered or when historical data is retrieved. The task is classified into two categories: planned maintenance and unanticipated maintenance. Unplanned maintenance includes all chores that cannot be predicted in advance, such as an unexpected failure.
Request: The work details are compiled and forwarded to the maintenance team for further action.
Schedule: The next step is to schedule the work orders that have been requested. Work orders might be scheduled according to a predetermined deadline, anticipated maintenance triggers, or dedicated time blocks. Setting a deadline holds everyone accountable and keeps everyone informed so that nothing falls between the cracks.
Assign: The work order is assigned to a technician, who completes the task. This can be a five-minute check of equipment, or it can be a complex repair job that takes several days.
Documentation: The next step is to schedule the work orders that have been requested. Work orders might be scheduled according to a predetermined deadline, anticipated maintenance triggers, or dedicated time blocks. Setting a deadline holds everyone accountable and keeps everyone informed so that nothing falls between the cracks.
Analyze: Work orders that have been closed include useful information. They can provide insight into your processes and systems that can be leveraged to improve your business. A repair order log also allows personnel to immediately identify any missed steps or different remedies if an issue reoccurs.
To Conclude
Work orders are an essential component of good maintenance. A well-designed maintenance work order and work order workflow facilitate the establishment of a preventative maintenance programme and the response to unplanned repair. A work order, when correctly managed, provides your team with the consistency and structure it requires to be efficient. Furthermore, it simplifies and streamlines all of the processes.