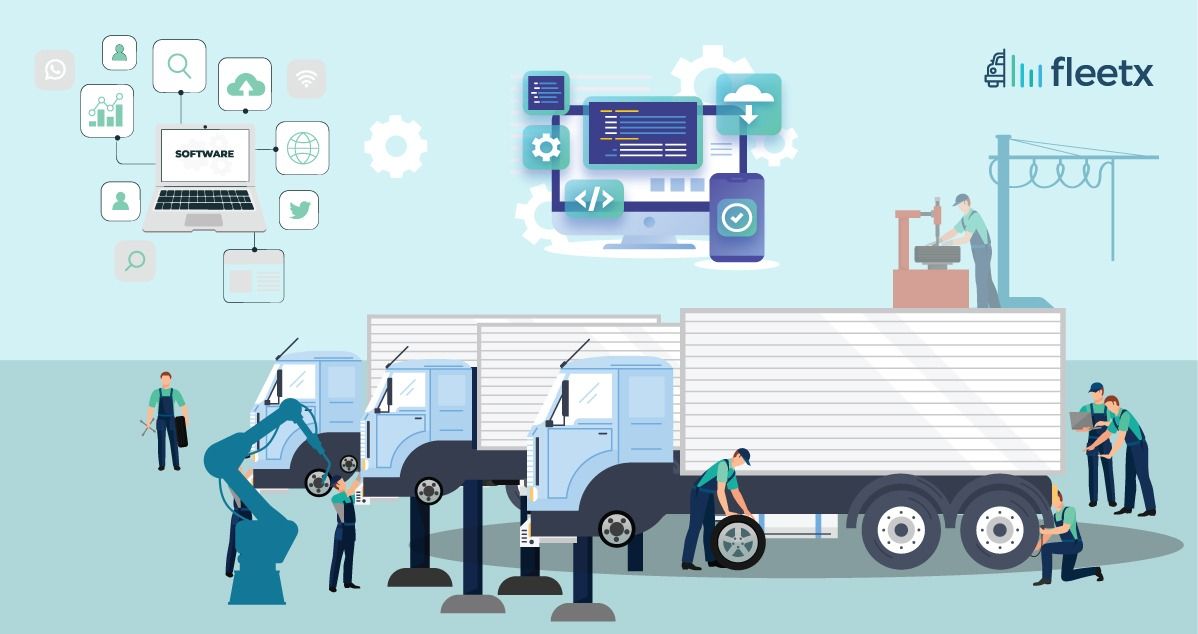
Preventive maintenance is an important component of every transportation operation. The goal of an effective preventative maintenance programme is to forecast problems and extend the life of equipment and tools. The procedure ensures the company's dependable and efficient functioning by ensuring that equipment does not fail when it is needed.
Its effectiveness and efficiency are dependent on seven key components. Also, adoption of good preventative maintenance software is critical because unreliable and erroneous data affect manufacturing quality, resulting in unforeseen repair expenditures and emergencies.
With properly integrated software and following preventive maintenance, the organization can maximize asset health and reduce equipment breakdowns, enhancing productivity and optimizing costs. Effective preventive maintenance has seven important components. Testing, servicing, calibration, inspection, adjustment, alignment, and installation are the seven elements of a preventive maintenance plan, which are explained below:
Inspection: It is critical to check the condition of assets on a regular basis in order to determine their value and future requirements. Inspections should be planned, and physical, mechanical, electrical, and other inspections should be performed as needed.
Servicing: Vehicle and asset servicing is vital and should be performed on a regular basis to minimize premature wear and failure. Servicing assets and equipment, which includes cleaning, lubricating, charging, and so on, should be done and recorded since it is critical for a company to preserve records of previous maintenance. This allows the maintenance staff to know exactly what type of servicing is required and when it is required.
Calibration: Preventive maintenance helps determine the worth of an asset's (equipment's) or vehicle's qualities on a regular basis by comparing them to the expected standard made available by either the manufacturer or experts. It entails comparing the two, one of which is a certified standard with known precision, in order to detect and correct any discrepancy in precision between the asset being compared and the established certified standards.
Testing: It involves constantly testing and inspecting to ensure serviceability and to detect and track component degradation.
Alignment: Aligning the vehicle is required, but it can also include making modifications to an asset's defined variable parts in order to achieve peak performance.
Adjustment: To achieve optimal system performance, specified variable aspects of an asset may be modified on a regular basis.
Installation: To avoid breakdown and preserve the desired system tolerance, limited-life components or assets exhibiting time cycle or wear degradation should be replaced and installed prior to failure during the maintenance process.
Major components of a fleet preventive maintenance programme
Service Reminders: Most fleet managers develop maintenance schedules entirely based on odometer (kilometer basis) changes. Tracking meter readings for all assets in your fleet is critical to ensuring that assets receive the service they require on schedule. However, because many firms continue to employ paper systems, fleet managers may receive occasional and frequently wrong odometer updates. That is why, rather than relying on a kilometer basis, a systematic service reminder is required.
Service Programs : Preventive maintenance activities change depending on the type of vehicle. Creating service schedules for each asset in your fleet is time-consuming and laborious. To assist standardize and document schedules and reminders for each asset in your fleet that requires preventive maintenance, you will need service programmes that will produce and manage service reminders across assets.
Inspection: The knowledge obtained during frequent inspections drives an effective preventive maintenance programme. Routine inspections, such as the daily vehicle inspection, saves time when developing a preventative maintenance schedule. Inspections can take place during yard checks, at fueling stations, or at a predetermined time. When you know an inspection has been performed and what maintenance is required, make a note of it and add it to the maintenance calendar.
Inventory Management: Optimizing your parts and inventories contributes to a cost-effective and efficient fleet preventative maintenance programme. You must ensure that you have an adequate supply of the most regularly used maintenance items, such as fluids, hoses, belts, and filters.
Reports : Whether you perform preventative maintenance in-house or outsource it to a third party, it is critical to have reliable data and exploit the available data to track the performance of your programme. Major maintenance work can be prioritized by looking at past data on services done.
What feautures should a good fleet preventive maintenance software provide?
Automated scheduling: Tasks, work orders, scheduling, reminders, workflows, and tracking work orders should all be simplified and automated by the software. It should automate and store all data-related processes. Handling purchases, keeping vehicle inspection records, and managing inventories can all be made easier with these features.
Maintenance and service reminders: In preventative maintenance plans, the software should have a notification and alerts option. Based on your predefined parameters, it should automatically remind you of impending scheduled tune-ups, cleaning, servicing, and other upkeep operations. You can stay on top of repairs, manage labor schedules, and guarantee that all fleet vehicles receive proper maintenance with automated maintenance reminders.
Data and reports: The software should enable and simplify the reporting of services, inspections, and defects with a predefined set of problems. It will enable drivers and fleet managers to quickly complete their inspection and record the data. It will save time as well as maintain accuracy and flow in the operations.
Analytical insights: The software should monitor and provide all the analytical information about the vehicles.
Remotely accessible: The software should be mobile and should allow fleet managers to access it remotely on their mobile phones or laptops, this will enable them to take quick actions and allow them to instruct regardless of their location.
Conclusion
Preventive maintenance is an essential component of infrastructure management, contributing to increased equipment lifetime, decreased unscheduled downtime, and, ultimately, lower long-term maintenance costs. As previously discussed, practicing preventative maintenance in a fleet business extends the life of the fleet while lowering maintenance and repair expenses. While beginning a preventative maintenance programme may appear hard at first, picking the proper software according to their needs can simplify it, help decrease labor expenses, and reduce overall maintenance inaccuracies.