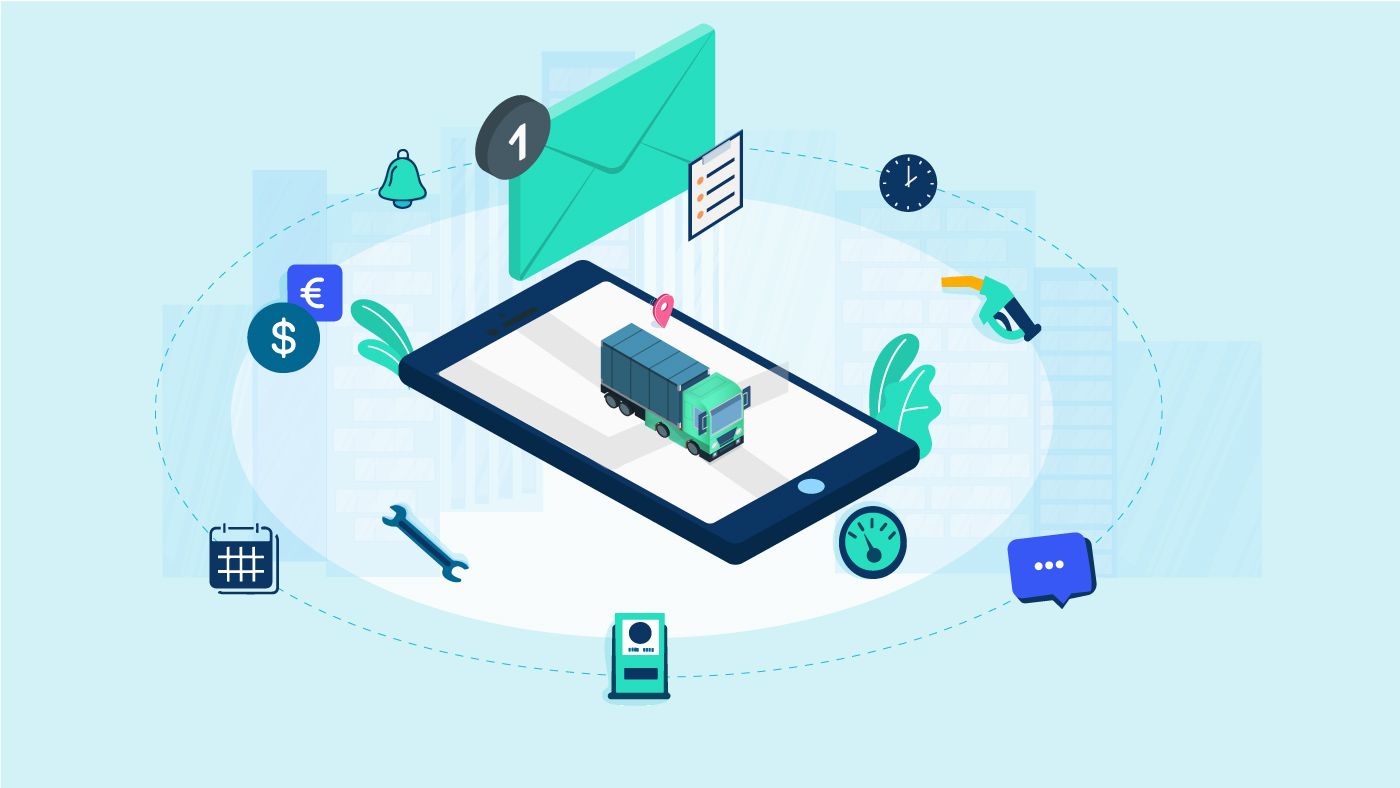
Keeping up with the maintenance needs of a fleet can be quite a daunting task, especially when the fleet manager has more than a dozen vehicles. Some of the major challenges faced are tracking and scheduling servicing requests, vehicle renewal reminders, pollution & fitness certificates and permit renewals among others. Taking cognizance of such a challenge, Fleetx is working with clients to solve problems by boosting productivity and limiting downtime.
As per Mckinsey’s Report Resilience in transport and logistics, companies in the Transport and Logistics (T&L) sector suffer more than their counterparts in other industries, during an economic slowdown. It is only when a T&L company is “resilient” that it can outperform industry averages. The report narrows down essential aspects of this “resilience” framework and highlights “process automation” as one of four key drivers of such companies. The process automation includes daily scheduling, task allocation and automating maintenance tasks. The report points out that such a technology can reap benefits upto 15% in maintenance efficiency and about 25% in service level misses.
Realizing such an immense potential of automating maintenance tasks and helping clients in improving efficiency, Fleetx has developed the Reminders module well integrated within FMS & ERP systems. We reached out to Fleet Managers who faced difficulty in managing a system of reminders - be it related to servicing, vehicle permits, environmental certificates or people-related issues such as license expiry and training reminders. This enabled us to provide a comprehensive yet adaptable module that caters to the industry's needs. Let us see how fleet managers can use this module to drive efficiency and limit downtime.
Each manager account in Fleetx is provided with three options.
- Service Renewal Reminders
- Vehicle Renewal Reminders
- Contact Renewal Reminders
Service Renewal Reminder is for recurring servicing requirements of vehicles which can prove costly if forgotten. The module comes with an option of creating single or multiple reminders at one go using an interactive menu. Clients have the option to create service reminders: distance-wise or time-wise. In addition to this, one can also specify thresholds for notifying if a reminder is “due soon”. The system has inbuilt support for web, SMS and e-mail notifications throughout the user hierarchy in a client’s ecosystem.
Top uses of Service Reminders:
Vehicle Renewal Reminder comes handy for those clients who wish to track different compliances related to vehicles such as fitness & pollution certificates, insurance and so on. The traditional method of keeping these in spreadsheets and notebooks while relying on phone calls had an adverse impact on management efficiency within the industry. Thus, the vehicle renewal reminder has become one of the most used features within the reminder module.
Top uses of Vehicle Renewal Reminders:
Contact Renewal Reminders is for those fleet managers who wish to streamline tasks related to their drivers and other staff. This comes in handy when the fleet size becomes large and there are hundreds of users within one vertical, with a handful of metrics to be tracked for each user such as license expiry, certifications, medical checkups and so on.
Top uses of Contact Renewal Reminders:
All three reminders give Fleet Managers full control of whom to notify, when to notify and by what medium to notify. Assessing the bulk requirement, Fleetx also provides a bulk uploader option through csvs thus enhancing efficiency.
Key benefits of using automated reminders
Opportunity cost of traditional methods
Traditional methods like using notebooks, whiteboards work well but are not scalable enough. Computerized tools such as spreadsheets, e-mails, calendars often are scalable but are not connected with each other.
Both the systems have inherent limitations in the form of opportunity cost while managing a large fleet. One of our Case Study explains that a client was able to save 3000 man-hours in 2.5 years thanks to more accurate, time-based maintenance rationalization.
Efficiency and Timeliness of Tasks
A common recurring problem in the logistics industry is a large backlog of maintenance tasks. These backlogs push teams to decrease efficiency in order to get things done quickly.
Reduction in quality of maintenance tasks results in reduced lifecycle of Fleet and increases pace of asset depreciation in the long run. Such delays can also have an impact on timeliness of operations, and can reduce efficiency making business unprofitable.
Arresting cost of unwanted breakdowns
Poor maintenance practices can cause instability and can be detrimental to business operations in the long run. Malfunctioning parts, vehicle breakdowns, expired certificates can become costly affairs for companies- both in terms of money and in time. Although nothing lasts forever and every piece of equipment has its lifecycle, with proper maintenance planning one can ensure that costs of unwanted breakdowns are minimized as much as possible.
In capital intensive industries such as transportation and logistics, asset maintenance holds a key importance in quality assurance.
As said by John Ruskin,
“Quality is never an accident, it is always the result of intelligent effort”
there is an imminent need in the industry to adapt best practices and cost effective technological solutions to asset maintenance. Fleetx stands committed with the industry in general and its partners in particular in order to drive efficiency and quality in India’s Logistic Sector.
How do I keep track of fleet maintenance?
A checklist should be created for preventative maintenance. It's an excellent way to check off things like fluid leaks, mirrors, cooling systems, seat belts, and other things that need to be examined and given special attention.You can track what needs to be examined and maybe fixed by keeping an exact record of all fleet maintenance and failures.
Which of the maintenance strategy should be the base for fleet management?
The easiest strategy to lessen, if not completely eliminate, vehicle breakdowns for fleets is through preventive maintenance. Preventive maintenance is calculated based on the amount of fuel used, mileage, time, or engine hours. Preventive maintenance plans set off procedures including vehicle inspection, cleaning, testing, repairs, part replacement, lubrication, and other continuing vehicle maintenance procedures when pre-defined criteria are reached.