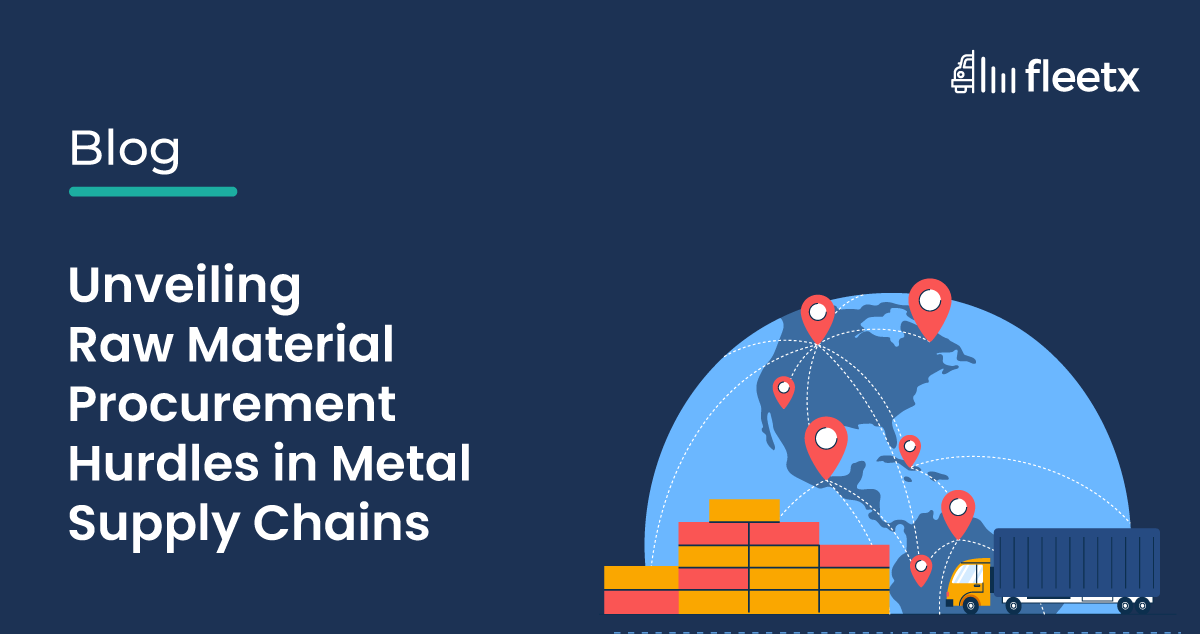
Last time around, we took a dive into the world of metals, uncovering the distinct yet equally captivating roles of precious and industrial metals. It was quite the journey! We discovered how precious metals, beyond their sparkle, act as our economic anchors in turbulent times. Then, we turned our attention to industrial metals, that form the very skeleton of our modern world. Revealing the complex supply chains that bring these metals from the depths of the earth right to our doorstep.
Moving on to a new chapter, This time we will be going through these essential materials from the ground to Metal manufacturing factories & warehouses.
Whether you're in logistics, procurement, or somewhere in between, we will be going through the raw material procurement process of the metal supply chain.
Raw Material Procurement in Indian Metal Manufacturing
Iron Ore: The Backbone of Steel Production
Iron ore is a critical raw material in the steel manufacturing process, and India stands as one of the leading producers globally. As of the latest reports, India's iron ore production reached 246 million tonnes in the fiscal year 2020-21. The country not only satisfies its domestic demand but also exports a significant quantity, with exports reaching around 46 million tonnes in the same period. The state of Odisha is the largest producer, contributing over 50% of the country’s total iron ore production.
Coal: Essential for Energy and Steel
Coal is another pivotal raw material, primarily used for power generation and as a reducing agent in steel production through the blast furnace route. India is the second-largest producer of coal, with an annual production of 729 million tonnes in the fiscal year 2020-21. The coal industry in India is dominated by state-owned Coal India Limited, which accounts for over 80% of the total coal production in the country.
Bauxite: Aluminium Production
For Aluminium, Bauxite is the primary raw material. India’s bauxite reserves are the fifth largest in the world, with an estimated reserve of over 3.5 billion tonnes. The production of bauxite in India was about 22 million tonnes in the fiscal year 2020-21, with Odisha again being the leading producer.
Procuring coal, iron ore, and bauxite to manufacturing plants in India presents significant logistics challenges, impacting efficiency and sustainability. Here's a concise overview:
Infrastructure Limitations
Road and Rail Congestion: Congested roads and rail networks, especially in mining regions, lead to delays. Limited port capacity further complicates the import and export of materials.
Geographical and Environmental Constraints
Remote Mining Locations: Mines are often in remote areas, increasing transport costs and carbon footprint. Seasonal weather, particularly monsoons, disrupts mining and transportation.
Regulatory and Compliance Hurdles
Environmental and Import Regulations: Stringent environmental laws and complex import regulations delay procurement processes, adding to logistics challenges.
Quality and Handling Issues
Handling and Storage: Specialized facilities are needed to maintain the quality of bulk materials, with inadequate handling leading to losses. Lack of supply chain visibility affects production planning.
Transportation Modes and Challenges
From a transportation perspective, the movement of raw materials like iron ore and coal to manufacturing plants involves complex logistics that can significantly impact the supply chain's efficiency, cost, and security. Here's an expanded view focusing on transportation issues:
Iron Ore Transportation: Iron ore is typically transported via rail or ship due to its bulk nature. Rail networks, being the backbone of iron ore logistics, often face capacity constraints and maintenance issues, leading to delays. Maritime transport, while effective for long distances, is subject to port congestion and shipping delays.
Coal Transportation: Coal also relies heavily on rail and road networks for domestic movement. The bulk transportation of coal is prone to logistical bottlenecks, especially in areas with inadequate rail infrastructure. Road transport, while more flexible, is affected by traffic congestion, road conditions, and higher costs.
Security Concerns and Theft
Theft during transportation, particularly of coal, is a significant issue. The high value and bulk nature of these commodities make them targets for theft, leading to losses and supply chain disruptions. Enhanced security measures, real-time tracking technologies, and strict regulatory enforcement are necessary to mitigate these risks.
On-Time Delivery and Its Importance
Manufacturing Dependencies: The timely delivery of raw materials is crucial for maintaining uninterrupted manufacturing processes. Delays in receiving iron ore or coal can halt production lines, leading to increased costs and missed deadlines.
Inventory Management: Efficient inventory management relies on predictable and consistent delivery schedules. Late deliveries force manufacturers to hold larger inventories as a buffer, tying up capital and increasing storage costs.
Impact of Delivery Delays
Operational Disruptions: Delays can disrupt the entire production schedule, affecting downstream operations and ultimately leading to delivery delays to customers.
Cost Implications: Late deliveries often result in rush orders, expedited shipping costs, and, in some cases, penalties for not meeting contractual obligations.
Customer Satisfaction: The inability to deliver finished goods on time can damage customer relationships and the manufacturer's reputation, potentially leading to lost business.
Mitigating Transportation Challenges
To address these transportation challenges, companies are investing in logistics planning and optimization technologies that offer better route planning, load optimization, and real-time tracking to enhance delivery predictability. Collaborating with reliable logistics partners and diversifying transportation modes can also reduce dependency on a single transport method, thereby mitigating risks associated with delays and theft. Furthermore, adopting just-in-time (JIT) inventory strategies, while maintaining a strategic buffer stock, can help manage the impact of delivery uncertainties.
The digitization of transportation logistics represents a transformative approach to managing the complexities of coal movement, ensuring compliance, and achieving on-time deliveries. By leveraging digital technologies, the coal industry can enhance efficiency, transparency, and security throughout the supply chain. Here’s how digitization plays a pivotal role:
Digital Tracking and Real-Time Visibility
GPS Technologies: The use of GPS tracking allows for real-time monitoring of coal shipments. This visibility enables proactive management of routes and immediate response to delays or disruptions, ensuring more reliable delivery schedules.
Automated Compliance Management
Digital Documentation and Reporting: Digitization simplifies compliance management by automating the creation, storage, and submission of necessary documents for regulatory compliance. Digital platforms can streamline permits, customs declarations, and environmental impact assessments, reducing the risk of non-compliance penalties and facilitating faster clearance processes.
Predictive Analytics for On-Time Deliveries
Forecasting and Planning Tools: Advanced analytics and machine learning algorithms can predict potential delays by analyzing historical data, weather conditions, and current traffic patterns. This predictive insight allows logistics planners to adjust schedules or routes in advance, minimizing the risk of late deliveries.
Enhanced Security and Theft Prevention
Security Monitoring: Digital technologies enable enhanced security measures for coal transportation. Surveillance systems and real-time alerts can deter theft and ensure the integrity of shipments from mine to plant.
Efficiency in Inventory Management
Integration with Inventory Systems: Digitization allows for seamless integration between transportation management systems and manufacturing plant inventory systems. This integration provides accurate, up-to-date information on material availability, helping to optimise inventory levels and reduce holding costs.
Conclusion
Integrating GPS for real-time tracking, streamlining compliance, and employing predictive analytics isn't just innovative—it's transformative. This approach revolutionises logistics, turning challenges into opportunities for reliable and timely deliveries.
Automating regulatory documentation isn't merely about compliance; it's a leap towards operational efficiency and reduced delays. Enhanced security with surveillance and alerts does more than deter theft; it protects our shipments, ensuring their integrity and bolstering confidence.
However, embracing digitization requires investment in technology, a commitment to digital literacy, and stringent cybersecurity measures. Achieving interoperability across diverse systems necessitates collaboration and standardisation among stakeholders.
Ready to Experience Our Product?
Book a demo today and discover how our product can benefit you.