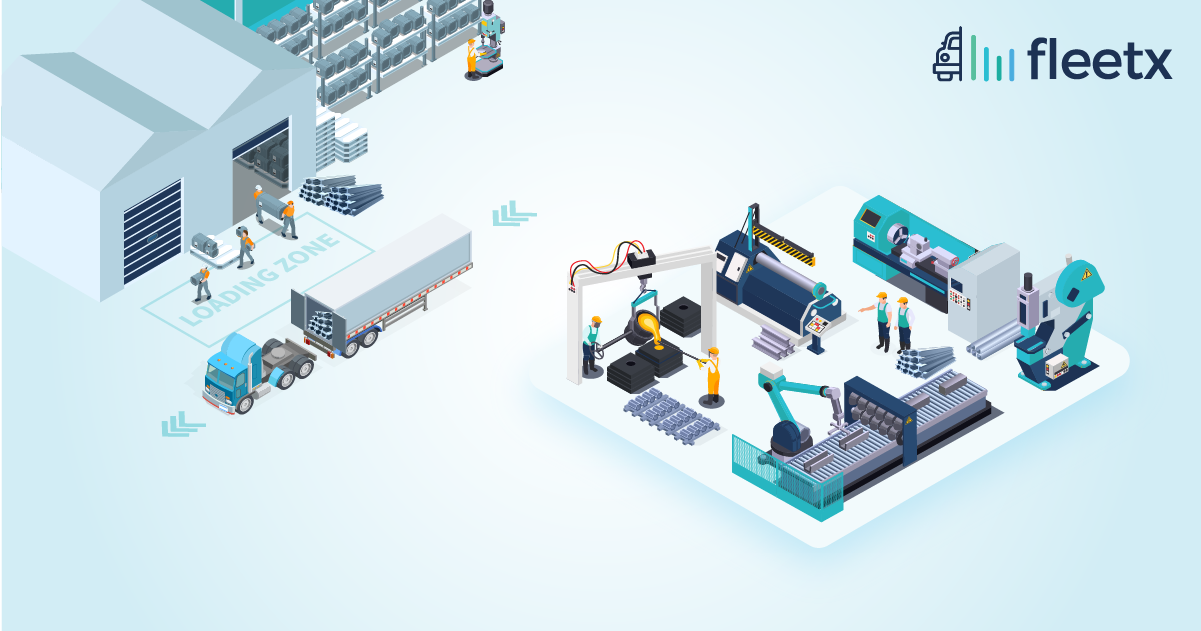
One of the major forces behind the industrial revolution has been metals. Steel has traditionally had a leading position among metals. Steel production and consumption are frequently used as measures of a country's economic development because they are both a raw material and an intermediary product. Since the steel industry is the foundation of every economy, it would not be an exaggeration to say that it has always been at the forefront of industrial progress.
India's leaders post-independence saw steel and power as the cornerstones of the country's future growth. Steel was used to build the majority of India's modern infrastructure, which confirmed their vision and solidified the sector's vital role in the growth of the country. India is currently on track to overtake Japan as the world's second-largest consumer of steel.
Steel is always in high demand in the worldwide market, but during the past two years, demand has grown at alarming rates, leading to shortages that are impacting the market. Concerns about having adequate steel for manufacturing demands in 2022 have been voiced by a lot of buyers. There are currently shortages due to problems in the supply chain, which have affected steel stocks and raised demand. A scarcity of steel has also been caused by transportation disruptions and mill shutdowns brought on by the spread of COVID-19 over the past two years.
The construction industry consumes half of all steel consumed worldwide, followed by the automobile and manufacturing industries. These industries' success is dependent on efficient and dependable supply chains. In addition, the steel sector must look into how emerging technologies can help it overcome some of its issues and how some of its challenges can be overcome by digitisation. The supply chain of the steel industry is a major obstacle in the steel industry's growth path. We list the seven main barriers that the steel industry faces to its growth prospects.
Rising steel demand and no proper way to supply it : Many steel mills are caught off guard by the unexpectedly quick rebound as they rush to meet the surge in demand. The pipeline used to ship components and raw materials to manufacturers all over the world jams as a result of this surge in demand. As steel is stacked up at ports due to the overflow of inbound ships, there is a scarcity of shipping trucks and improper truck usage. Add to that the fact that there is a labour shortage for plant workers, there has been no technological advancement, there are not enough truck drivers, and the shipping delays in the steel supply chain seem to have increased, creating a domino effect of production issues.
No proper logistics plan: Since logistics is the most crucial component of supply chain management, an appropriate logistics plan is required. The majority of Indian steel producers find it difficult, expensive, and difficult to manage their logistics needs. Iron ore is the main raw material used in the production of steel. Steel is a bulk commodity, and both steel and iron ore are bulk commodities. Therefore, moving bulk commodities is always difficult, whether it be physically moving steelmaking raw materials to steel mills or physically moving completed steel to demand areas.
In addition, unlike China, Japan, or Korea, where the majority of their steel plants are situated near the coast, India's steel plants are found inland. This makes it more difficult to manage the logistics needs of the majority of Indian steel producers.
The predominant means of transportation for steel producers are railroads and roads. Furthermore, it is economically unviable to move bulk commodities on roads. In conclusion, infrastructure bottlenecks, particularly in the connectivity of roadways, are another external challenge that may be more important than considerations for future growth.
Steel plants struggle to keep up with the demand: The inability of steel mills to keep up with the increased demand and limited technology is another issue with the supply chain in the steel industry. Due to the increased demand, steel companies have been compelled to run at significantly higher capacity than they typically do in order to satisfy these demands, making it more challenging to manage the entire supply chain process.
Numerous other variables make it difficult for steel mills to satisfactorily meet client demand. Lack of experienced staff and outdated technology are two such factors that make it tough for steelmakers to keep up with the trends of the day. Another effect of supply chain concerns is that operations now take longer than they should because of lengthened mill lead times and increasing demand.
Increased Steel Prices: All of the issues with the steel industry's supply chain have resulted in a significant increase in steel prices, and they have skyrocketed by 300 percent above pre-pandemic levels. Over the past year, the cost of producing steel materials increased by 141.6 percent, and the cost of producing iron and steel increased by 105 percent. Steel became more expensive to maintain as a result of the unreasonably high demand for the material, which led to shortages of raw materials and, in turn, factory inability to meet demand. The rising demand in the steel industry has produced supply chain issues, which has resulted in a significant increase in the price of buying raw steel. The lengthy and inaccurate supply chain procedure causes high demand and more cost. To meet the demand, it's important for the industries to have comprehensive plans and the latest technological advancements.
Unsafe delivery and unsafe unloading of steel products: While loading or unloading steel, people suffer severe injuries or even pass away every year. They are injured when loads are handled mechanically, when they fall off vehicles, etc. To lower the likelihood of accidents occurring, care must be taken by everyone involved in loading, delivering, and unloading trucks with steel. When it comes to loading trucks, it's crucial that the one chosen to move the steel load is adequate and built so that, given the nature of the road conditions, the load can be moved safely. A proper design for the truck's dimensions and structural integrity will promote driver security and secure steel unloading.
Driver safety and road safety: A few highly important factors when it comes to driver and road safety are long driving hours, poor road conditions, exhaustion , and driver distraction. The state of the roads makes it difficult to carry high-end steel products across India, which ideally travel 1700 kilometers from the manufacturing locations.
Since the aforementioned restrictions must be taken into account, it is necessary to employ driver safety and transport management systems that strive for the best delivery and cost while paying close attention to safety and the environment.
Weighbridge breakdown: In addition to the cost of repairs, a weighbridge breakdown can result in costly downtime, loss of production, delays, extra manpower, and errors in the loads of the steel industry or any other.
One of the most crucial components of the steel supply chain is the weighbridge. The best preventative measure a company can implement to reduce the likelihood of a weighbridge breakdown and maximise proper steel supply is preventative maintenance, ongoing inspection, and regular servicing of both the mechanical and electrical components of the weighbridge.
Path ahead
As India works to become a manufacturing powerhouse through legislative initiatives like Make in India, the steel industry has emerged as a major emphasis area given the importance of a multitude of industries on its output . The steel industry and the nation's export manufacturing capacity have the potential to help India reclaim its favourable steel trade balance. The country's steel industry needs to become more competitive immediately. Cost reduction across the supply chain, the development of effective logistics, and a reduction in finance costs are some of the steps needed to accomplish this.
Manufacturing companies that produce steel and metal are regarded as asset heavy. The steel sector is undergoing an exciting shift with the development of new emerging technologies like robotics, drones, and IoT that offer useful solutions to business. In addition to automating processes, these technologies link all of the components of a plant, enabling real-time interaction and increasing system efficiency. Labor productivity will also increase because of effective performance and technology integration. This will contribute to cost-cutting and an increase in industry profitability. Success in the future depends heavily on how developing technologies are adopted. A push from the government and the adoption of cutting-edge technologies will allow India to become a trillion dollar economy.
What is the supply chain of steel?
There are two components to the steel supply chain: Steel supply chain upstream: from mining to steel production. Storage of steel processing facilities, distribution, and processing to produce finished goods make up the downstream steel supply chain.
What is the manufacturing process of steel?
There are two processes in the production of steels. The basic oxygen furnace (BOF) method or melting scrap steel or direct reduced iron (DRI) in an electric arc furnace are both used to turn liquid iron into steel during the first stage of the steelmaking process. In the refinement process known as secondary steelmaking, alloying metals are added and impurities are taken out.