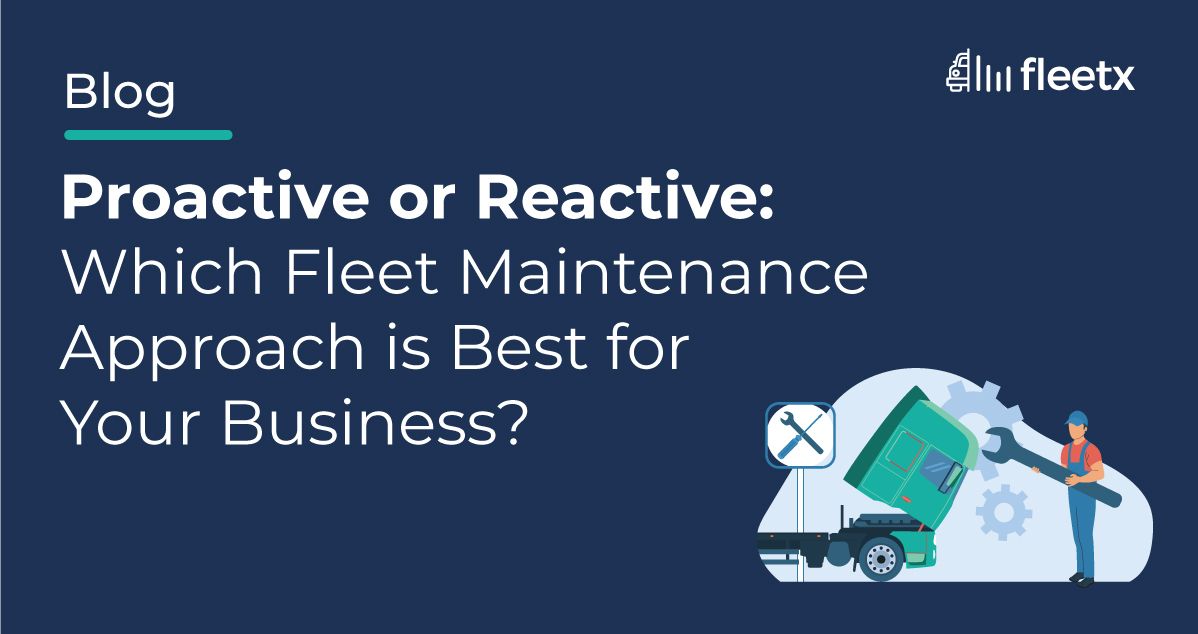
As the world becomes increasingly dependent on transportation and logistics, the importance of maintaining a reliable fleet of vehicles has never been greater. The transportation and logistics industry in India is no exception, where fleet operations must be seamless and effective in order to fulfill consumer needs and ensure timely delivery. However, maintaining a large vehicle fleet is a complex and expensive process, and there is no one-size-fits-all fleet maintenance solution. This is where various fleet maintenance approaches come into play, offering transportation and logistics companies with a variety of tools to successfully manage their fleets.
Fleet managers must adopt maintenance approaches to ensure the optimal performance and longevity of their fleet. With several benefits to gain, fleet managers invest in the right maintenance strategy tailored to their specific fleet and industry. Understanding the significance of alternative approaches to fleet maintenance is the first step to achieving a successful fleet management plan.
Additionally, when it comes to fleet maintenance, every fleet manager has their own set of rules and guidelines. Some prefer a preventive approach, while others opt for a predictive maintenance program. However, a well-rounded and successful business knows that utilizing a combination of maintenance approaches is more beneficial than sticking to one approach. Collaborating on different maintenance approaches can lead to reduced maintenance costs and downtime, improved vehicle lifespan, and increased safety and customer satisfaction. Therefore, fleet managers must be open to exploring and implementing new strategies and technologies to ensure their fleets run smoothly.
What is Proactive maintenance?
Proactive maintenance is a form of maintenance technique that focuses on recognizing and preventing potential problems before they arise, as opposed to waiting for them and reacting to them. This strategy entails performing regular inspections, testing, and replacing parts that are known to have a limited lifespan or are prone to failure. Proactive maintenance can prevent unexpected equipment downtime, increase equipment lifespan, and save total maintenance costs by recognizing and treating possible issues early.
Proactive maintenance is a preventative method that needs equipment to be monitored and inspected on a regular basis to maintain optimal operation. Fleet managers can discover faults before they become big problems by arranging frequent maintenance checks, decreasing the likelihood of unexpected breakdowns or downtime. This technique frequently includes replacing old or damaged parts, lubricating equipment, and testing important system performance. Fleet managers may take charge of their fleet's maintenance needs with proactive maintenance, ensuring that their equipment functions smoothly and efficiently, lowering costs and boosting overall fleet performance.
What is Reactive Maintenance?
Reactive maintenance is a maintenance technique that addresses equipment faults as they occur or after they have caused equipment failure. This method is often known as "breakdown maintenance" since it entails only repairing or replacing equipment after it has failed or broken down. Reactive maintenance can be costly since it frequently necessitates extensive repairs or the replacement of entire systems, resulting in unforeseen downtime and lost production. Furthermore, reactive maintenance can raise safety problems since it may necessitate the use of equipment that has not been sufficiently tested or maintained. However, in some cases, such as when unexpected equipment failures occur or resources are limited, reactive maintenance may be required.
While reactive maintenance might be effective in certain situations, it should not be used as a fleet's only maintenance approach. Instead, combining reactive maintenance with proactive and predictive maintenance procedures can assist ensure that equipment is functioning at top performance while minimizing unplanned downtime and maintenance expenditures.
Proactive Vs Reactive Fleet maintenance
While proactive and reactive maintenance approaches may appear conflicting, they can work together to build a well-rounded maintenance strategy. Reactive maintenance is frequently more expensive, with the average cost of a repair being up to four times that of proactive maintenance. Proactive maintenance, on the other hand, can prevent costly breakdowns and downtime, resulting in maintenance cost savings. To make educated decisions and achieve optimal maintenance outcomes, fleet managers must first understand the benefits and limitations of both techniques. Both proactive and reactive maintenance approaches have advantages and disadvantages, and the ideal approach is determined by the fleet's specific demands and goals, as well as the industries in which they operate.
- Proactive maintenance can help prevent equipment failures and extend the lifespan of assets, resulting in long-term cost benefits. However, it may necessitate a larger initial investment in terms of time, money, and resources because it entails regular inspections, repairs, and replacements of parts before they fail.
- Reactive maintenance, on the other hand, is useful when unexpected equipment problems occur when finances are restricted. In the near term, reactive maintenance can be a more cost-effective technique because it only handles issues as they arise. Relying only on reactive maintenance can result in higher long-term expenditures due to equipment breakdowns.
How do you choose between proactive and reactive fleet maintenance?
- Manufacturing, construction, and transportation industries, for example, are better suited to proactive maintenance because of the value of their equipment and continuous operations. This is because proactive maintenance can help prevent unexpected equipment breakdowns and increase equipment longevity, resulting in long-term cost savings. In these industries, regular inspections, maintenance, and replacement of parts before they fail can also help reduce the likelihood of safety risks.
- Reactive maintenance, on the other hand, may be better appropriate for industries with less expensive equipment or with restricted funds. In the near term, reactive maintenance can be a more cost-effective technique because it only handles issues as they arise. However, relying entirely on reactive maintenance can result in greater long-term expenditures due to unforeseen downtime and costly repairs.
To Conclude
Lastly, fleet maintenance is a critical component of the transportation and logistics business, and fleet managers must grasp the need to employ a variety of maintenance methods. While proactive maintenance can help to avoid costly breakdowns and lower maintenance costs, reactive maintenance is frequently required to deal with unforeseen equipment failures.
However, a balanced approach that combines both proactive and reactive maintenance approaches can help ensure that equipment operates at top performance while minimizing unplanned downtime and maintenance expenses. Fleet managers can use logistics automation solutions to monitor equipment performance in real time, foresee possible faults, and arrange maintenance schedules appropriately. This allows businesses to optimize the benefits of both preventative and reactive maintenance, resulting in greater safety, increased customer satisfaction, and lower company costs.