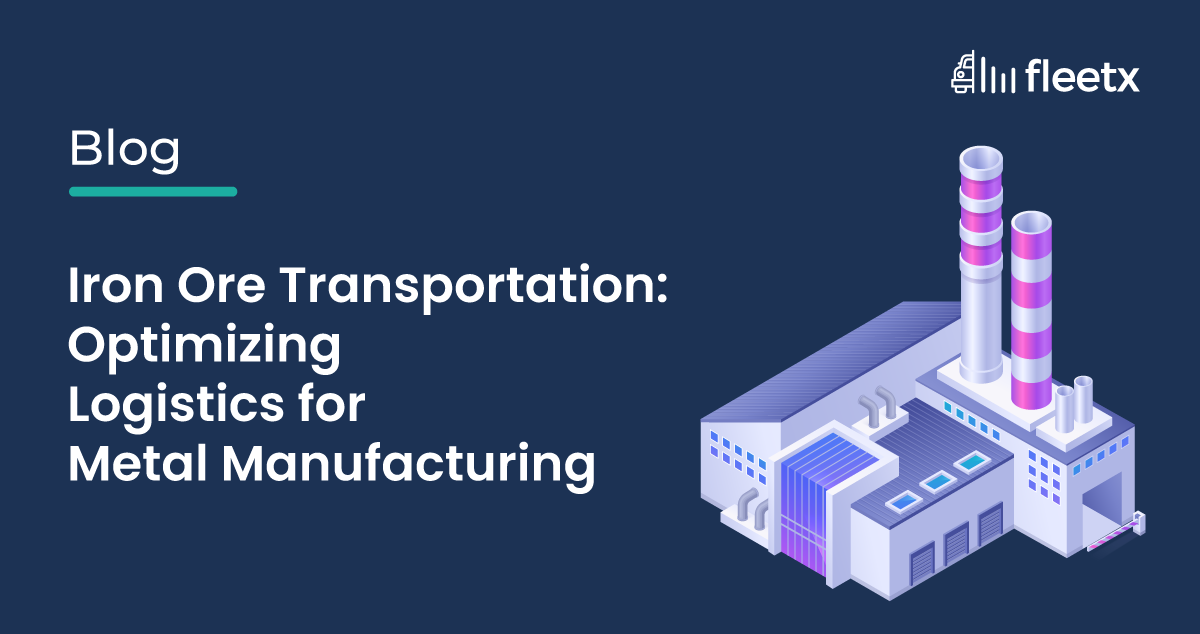
The iron ore industry is a cornerstone of the global steel market, with India playing a pivotal role in both production and export. This blog delves into the current state of iron ore in India, the primary modes of its transportation, with a focus on road logistics, and the challenges and solutions associated with this mode of transport.
State of Iron Ore: A Glance
Iron ore is indispensable in steel making, serving as the raw material that is transformed into steel, an alloy that forms the backbone of the infrastructure and manufacturing sectors globally. In 2007, the world saw iron ore production soar to 1.60 billion metric tons, marking a six-year sequential increase driven by the global steel boom. Leading this surge were Brazil, China, Australia, and India, with Brazil and Australia dominating global sea trade in iron ore, accounting for a significant portion of the 822.40 million metric tons traded by sea that year.
India, not to be overlooked, has shown remarkable growth in both production and exports of iron ore. From 1996 to 2007, production ramped up from 66.60 million metric tons to 206.90 million metric tons, while exports grew from 31.70 million metric tons to 104.00 million metric tons. This growth trajectory underscores India's capacity to meet both domestic and international demand, with projections for 2011-12 indicating a production of 242 million metric tons, aligning closely with domestic consumption and export levels.
Iron Ore's Journey: From Mine to Manufacturing
The transportation of iron ore in India employs various modes, notably railways, roadways, and waterways, each playing a crucial role in the supply chain. However, road transport, despite facing significant challenges, remains a vital link, especially for regions where other modes are less feasible.
The Road Logistics Challenge
Road transportation, carrying 65% of all freight in India, faces issues of congestion, poor road quality, and a lack of professionalism due to the dominance of small-scale fleet owners. This inefficiency in the logistics network not only escalates costs but also impacts the timely delivery of iron ore to manufacturing plants.
Statistical Insights into Road Transportation
National Highways, while only 2% of the road network, handle about 40% of traffic.
The road sector has seen vehicle numbers grow at an average pace of 10.16% annually.
Highways often lack the necessary multi-laning, with 56% being single-lane roads, leading to severe bottlenecks.
The Predominance of Road Transportation
Road logistics are vital in India, with 65% of all freight and 80% of passenger traffic carried by this network. Although national highways constitute only 2% of the road infrastructure, they handle about 40% of the traffic. The distribution of road lanes varies, with a mix of four-lane, double-lane, and single-lane roads facilitating the movement of goods across the country. However, the growth rate of vehicles, averaging 10.16% per annum, points towards increasing reliance on road transport for logistics needs.
Challenges in Road Transportation
The road transportation of iron ore is not without its hurdles. Highways often face congestion and are not adequately multi-laned, leading to bottlenecks and delays. The quality of road surfaces and the lack of maintenance further exacerbate these challenges. Additionally, the road transport sector is dominated by small-scale fleet owners, which hinders professionalism and efficiency. The absence of industry status for road transport operators limits their access to low-interest rate funds, restricting their capacity for investment and improvement.
Congestion and Infrastructure Limitations
One of the major hurdles is the congestion on highways, many of which are narrow and lack multiple lanes. This congestion is exacerbated by the sheer volume of traffic, as roads are the predominant mode of transport for both freight and passengers in India. The national highways, although carrying about 40% of the traffic, are only 2% of the road network. With iron ore being a heavy and bulk commodity, the need for efficient road networks is paramount. The existing infrastructure, with a distribution skewed towards single-lane roads (56%), is inadequate to handle the volume and weight of iron ore trucks, leading to delays and increased transportation costs.
Poor Road Conditions and Maintenance
The quality of road surfaces and the level of maintenance are far from satisfactory. Poor road conditions not only slow down the movement but also increase wear and tear on the transport vehicles, elevating the operational costs for fleet owners. This situation is further strained by the fact that maintenance needs are only one-third met, pointing towards a significant infrastructure deficit.
Impact of Disrupted Supply Chain on Steel Manufacturers
The supply chain disruptions in the transportation of iron ore have a domino effect on the steel manufacturing industry. Iron ore is the lifeline for steel plants, and any hiccup in its supply chain directly impacts production schedules, costs, and ultimately, the market supply of steel.
Production Delays and Increased Costs
Delays in the arrival of iron ore due to road transportation challenges lead to production slowdowns or even halts, affecting the steel manufacturers' ability to meet delivery commitments. The increased transportation costs, due to inefficiencies and extended transit times, also inflate the production costs. These additional costs may be passed on to the consumers, affecting the competitiveness of Indian steel in the global market.
Inventory and Storage Issues
Steel manufacturers are forced to maintain higher inventory levels to buffer against supply chain disruptions, tying up capital that could otherwise be used for expansion or modernization. Storage issues also arise, as space must be allocated for these larger inventories, further increasing the operational costs.
Quality Degradation
Prolonged storage and exposure to elements due to delays in transportation can degrade the quality of iron ore. This degradation affects the quality of steel produced, posing challenges in meeting the stringent specifications required by certain industries or export markets.
Environmental Impact
The inefficiencies in road transport lead to increased fuel consumption and emissions, contributing to the environmental footprint of steel production. This aspect is increasingly significant given the global push towards sustainability and green manufacturing practices.
The seamless production of steel heavily relies on the timely delivery of iron ore to manufacturing plants. Delays in the arrival of this essential raw material can have cascading effects on the operational efficiency, cost structure, and overall competitiveness of steel manufacturers. Recognizing the implications of such delays is crucial for implementing effective solutions.
Impact of Raw Material Delay
Production Inefficiencies: Any hiccup in the supply of iron ore can lead to production bottlenecks, disrupting the entire manufacturing schedule. This inefficiency not only reduces output but also affects the ability to fulfill orders on time, potentially harming relationships with clients and market reputation.
Increased Operational Costs: Delays often necessitate expedited shipping methods or the purchase of materials at premium prices to meet production deadlines, significantly increasing operational costs. These unexpected expenses can erode profit margins and affect the pricing strategy of the final product.
Inventory Management Challenges: To mitigate the risk of supply chain disruptions, manufacturers may resort to maintaining higher levels of inventory. While this approach provides a buffer, it also ties up capital that could be used more effectively elsewhere in the business.
Quality Control Issues: The quality of iron ore can be compromised if delays result in prolonged storage, especially under unsuitable conditions. Such degradation can affect the quality of steel produced, leading to potential customer dissatisfaction and reputational damage.
When Iron Ore Doesn't Show Up on Time
The ripple effects of iron ore delivery delays stretch far, affecting production schedules, bumping up operational costs, and complicating inventory management. Steel manufacturing is highly sensitive to raw material availability, with any delay causing notable disruptions.
Tech to the Rescue: Real-Time Tracking and Geofencing
Adopting real-time tracking and geofencing tech offers a glimmer of hope. These tools provide live updates on the whereabouts of iron ore shipments, enabling better route management and scheduling. With GPS and IoT tech, steel manufacturers can gain better visibility and efficiency in their supply chains, minimizing delays.
The Upsides of Going Digital
Better Operational Efficiency: Real-time tracking allows for quick adjustments in production, reducing idle times and boosting output.
Cost Control: Optimizing routes and cutting down on delays significantly lowers the cost of moving iron ore.
Quality Keeps Up: Ensuring iron ore arrives on time helps maintain its quality, which directly affects the steel's quality.
Wrapping Up
The journey of iron ore from mine to manufacturing is complex and fraught with challenges, especially across India's vast and diverse landscape. However, strategic interventions and embracing technology can streamline road transport. Real-time tracking and geofencing don't just promise to ease logistical headaches; they also pave the way for a more resilient and competitive steel industry. As we look ahead, focusing on infrastructure improvements and tech adoption will be crucial in overcoming the hurdles of iron ore transportation, ensuring a steady flow of this essential material to steel plants across the country
Ready to Experience Our Product?
Book a demo today and discover how our product can benefit you.