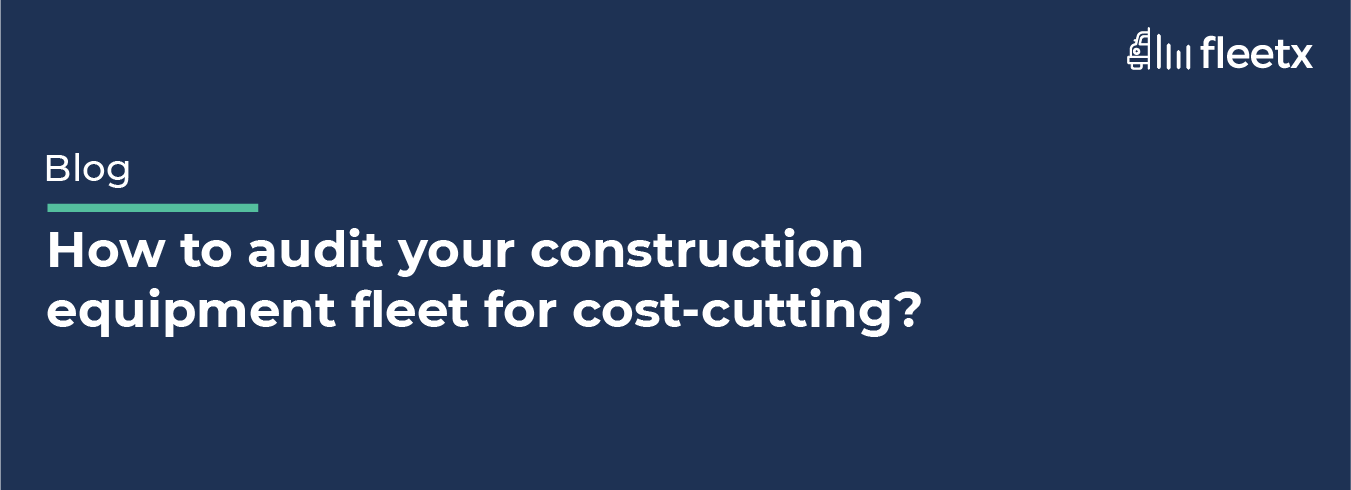
Construction vehicles and equipment are a huge investment for companies in this industry. Additionally, the constantly changing and evolving conditions of the construction sector make it even more difficult to receive investments and increase profitability. Ensuring that your business is always on top of its game by cutting costs without sacrificing productivity or efficiency is the need of the hour.
Construction Equipment Management software is critical in reducing wasted time and money. This valuable solution can empower better management of your construction equipment and commercial trucks, ultimately improving operations. Using such an efficient Construction Equipment Management system optimises daily processes for your company as well as aims to do more work at a reduced cost.
Maintain machine uptime and health for lesser operating costs
Machine uptime is critically important for construction businesses, which is why their health is of utmost importance. Equipment that has been well-serviced on time and is capable of performing at its highest capacity is the only way to ensure smooth running. On the other hand, without such a continual and constant tracking of machine or equipment health, you may face unnecessary breakdowns and increase operating costs considerably. You will also get more reliable performance with increased efficiency by monitoring factors such as machine utilisation rate, equipment ageing, active working time, depreciation, and more.
Planned maintenance to keep equipment in check
Planned maintenance refers to a continual check on equipment or machinery to ensure there are no major malfunctions or problems happening. The aim is to prevent these problems through periodic checks to reduce unplanned machine breakdown as well as prevent downtimes in production.
Using Construction Equipment Management software can help businesses do more with less. It helps keep track of the vehicle and equipment and alerts the concerned personnel of any latencies or internal issues much before the machine breaks down. This kind of preemptive planning ensures that servicing and parts are changed without delay and the machine is not rendered useless or broken beyond repair.
Preventive and unplanned maintenance for emergencies
Construction equipment and vehicles that are regularly checked on and maintained have a lesser chance of causing accidents, thus instantaneously reducing unforeseen operating and repair costs. Telemetry integration as well as the use of IoT technologies (RFID, Geo-fencing, and such) help in adding that much-needed extra protection and awareness. Even with a complete plan for maintenance, there are times of unscheduled downtime, thus requiring preventative or unplanned maintenance that may become costly. Additionally, maintenance over-time can also lead to more costs incurred.
Minimised risk and better safety to eliminate theft
All your construction equipment and vehicles need to be in their best shape and be usable for projects, employees, and more. Construction Equipment Management software allows you to keep track of your equipment usage and responsibility levels, as well as monitors improper usage that may lead to additional costs. This insight helps avoid risks and keep track of your contrition equipment by knowing where, how, and when it was last used. It is also a factor that helps in preventing equipment theft, which is a huge problem in the construction industry and costs businesses a lot of money each year.
Minimising risks is a safe way to reduce costs as it allows things to run smoothly and eliminate unnecessary accidents. Reduce personnel injuries and keep your equipment in working order as it also improves equipment profitability. Life-long cost tracking allows for guaranteed accountability as well as compliance with legal regulations.
Keep track of rising and unnecessary fuel costs
Keeping construction machinery and vehicles fueled is a very expensive proposition, especially since petrol prices are at an all-time high. On top of that, fuel theft and unauthorised or incorrect usage of vehicles can only add to rising costs. With Construction Equipment Management software you can integrate fuel automation systems that help in identifying machinery that has a high fuel consumption. This lets you take quick actions to correct usage and personnel mistakes as well as take the necessary precautions without facing any loss.
Conclusion
Construction Equipment Management Systems for equipment rental services or construction companies have become an indispensable need for construction businesses as they offer sophisticated control over equipment vehicles. Using its cutting-edge technology such as Geo-fencing, telematics, fuel automation, and more can not just help maintain equipment but also prolong its life using a cost-efficient approach. Get real-time tracking for vehicles or machinery location, as well as deep insight into each equipment’s data allowing you to make more accurate decisions.
Keeping a track of percentage of preventive maintenance hours, percentage of reactive maintenance hours, percentage of maintenance overtime hours, maintenance cost as a percentage of revenue, maintenance cost as a percentage of estimated replacement value, equipment financial utilisation, and more - factors that are all beneficial for cost-cutting in your business.
What is an equipment audit?
Equipment Management conducts annual audits to confirm inventory. Audits are carried out to check the CAMS records and the equipment, and to make sure that the equipment policy and procedure are being followed.
What conditions of tools machines and equipment should be considered during regular checking and inspection?
An inspection's goal is to determine if work equipment can be used, adjusted, and maintained properly. Any deterioration should be identified and fixed before it poses a risk to health and safety.