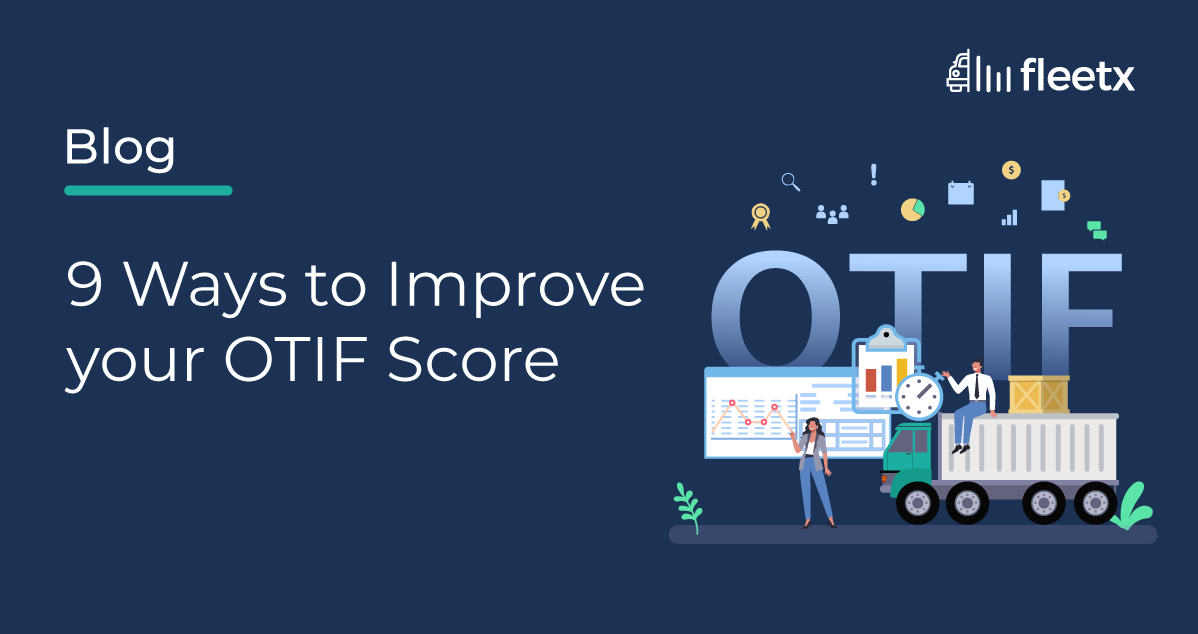
Improving an OTIF score requires a systematic approach that involves identifying and addressing the key factors that are impacting delivery performance. This article will discuss some of the challenges that limit a company’s delivery performance in India, as well as some of the current best practices in the industry to improve the OTIF score.
The logistics industry in India faces unique challenges that can impact the OTIF score:
Infrastructure Constraints: India's logistics infrastructure, including road networks, railways, and ports, is often stretched and inadequate to meet the demands of the growing economy. Poor infrastructure can lead to delays in transportation and affect the on-time delivery of goods.
Last-Mile Connectivity: The last-mile delivery is a significant challenge in India, especially in urban areas with congested traffic and narrow streets. Ensuring timely delivery to the final destination can be complex, and logistics companies need innovative solutions to overcome these hurdles.
Regulatory and Taxation: India has a complex regulatory and tax system, including state-level taxes and permits. Complying with these regulations and managing paperwork can sometimes cause delays in goods movement.
Inventory Management: Inventory management practices, including stock-outs and overstocking, can affect the ability to fulfill orders in full and on time.
Seasonal Demand Variations: India experiences significant seasonal variations in demand, such as during festivals and peak shopping seasons. Logistics companies must prepare for these spikes in demand to maintain a high OTIF score.
Strategies to Improve OTIF score
Improving the score of a company will take planning, and addressing the problem holistically. It might take time to see changes in the OTIF score in the short-term, but it is sure to pay off in the long run. Here are some things to look at:
- Effective planning and forecasting: Ensure accurate demand forecasting and inventory planning to have the right products available when needed. Utilize data and historical sales patterns to anticipate customer demands and avoid stockouts.
- Streamline order processing: Optimize order processing systems to reduce manual errors and delays. Implement automated order processing and use barcode scanning and RFID technology to improve accuracy and efficiency.
- Improve collaboration with suppliers: Work closely with suppliers to improve the reliability of incoming materials. Set clear expectations regarding delivery schedules and quality standards. Strong partnerships with suppliers can lead to better coordination and fewer delays in the supply chain.
- Efficient warehouse operations: Improve warehouse management to minimize order fulfillment time. Optimize the layout, use technology like warehouse management systems (WMS), and implement best practices for picking, packing, and shipping.
- Effective transportation management: Choose reliable carriers and optimize transportation routes. Utilize transportation management systems (TMS) to track shipments in real-time and avoid delays.
- Real-time visibility: Implement systems and technologies that provide real-time visibility into the supply chain. This helps identify potential issues early on, allowing for quick resolution and proactive communication with customers to manage expectations.
- Identify KPIs and implement continuous monitoring: Set key performance indicators (KPIs) related to OTIF and regularly monitor them. Analyze data to identify trends, root causes of delays, and proactively address the problems.
- Smooth customer communication: Keep customers informed about their order status and any potential delays. Transparency and proactive communication can help manage customer expectations and reduce the impact of unforeseen disruptions.
- Utilize technology: Leverage emerging and innovative technologies to help solve organisational challenges. The options are aplenty; AI-driven analytics, Internet of Things (IoT) devices, tracking technology, ERP systems, etc.
The Bottom Line
Just remember, improving the OTIF score is an ongoing process. It requires commitment from all levels of the organization, regular evaluation of performance metrics, and a willingness to adapt to ever-changing market conditions and customer needs. By identifying root causes of a low OTIIF score, and implementing these strategies, logistics companies can enhance their delivery performance, increase customer satisfaction, and gain a competitive advantage in the industry.