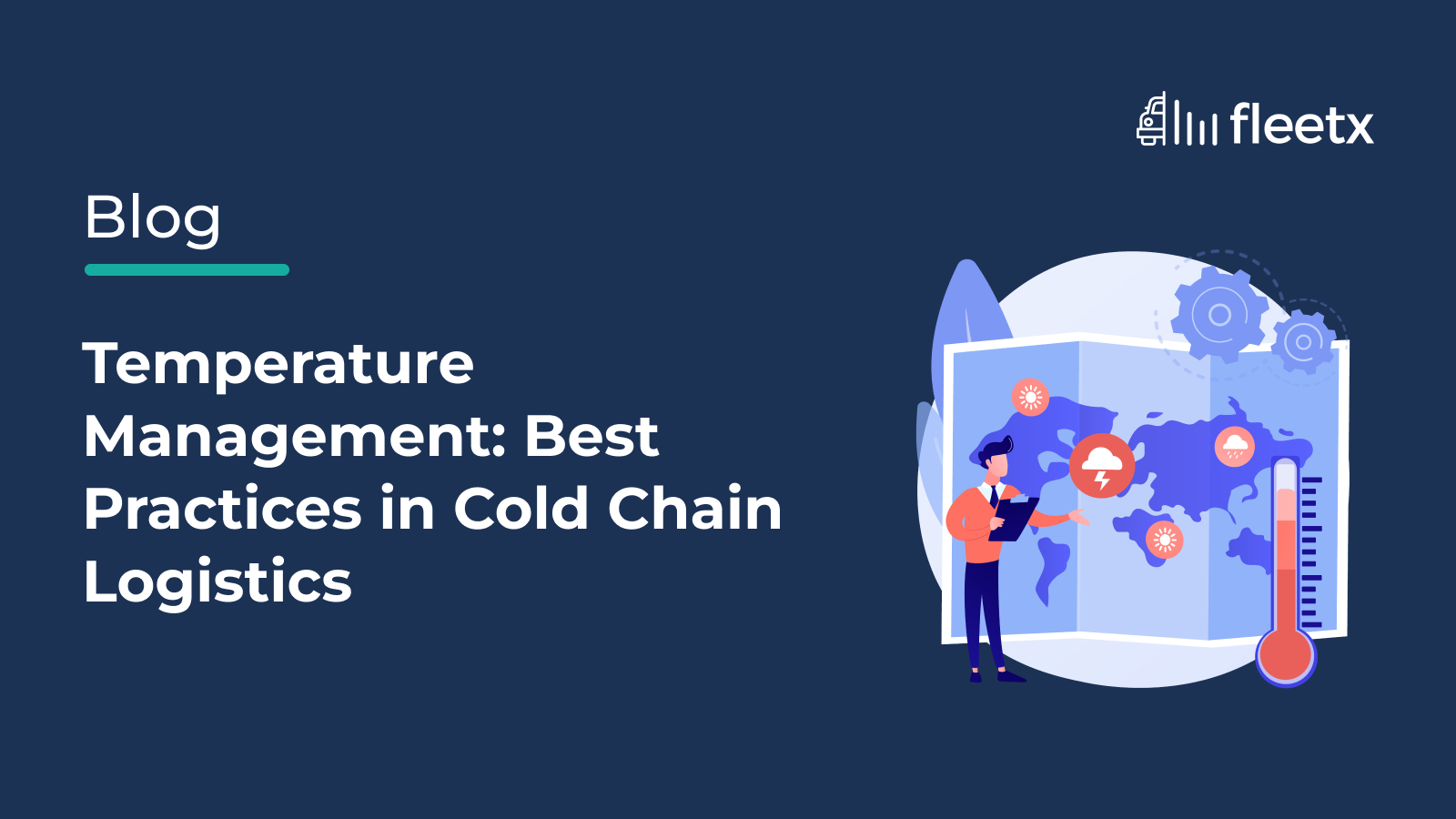
Cold chain logistics are essential for industries like food, pharmaceuticals, and agriculture to transport their products. Maintaining an unbroken temperature-controlled supply chain ensures the quality and safety of these perishable goods. However, the process is often challenging; in a country like India, with its temperate to tropical range of climate, and several infrastructure gaps, cold chain logistics operations often risk disruptions.
Cold-Chain Logistics in India: An Overview
The cold chain logistics sector in India is experiencing significant growth, driven by increasing demand for perishable goods and advancements in technology. In 2022, the industry was valued at approximately $7.2 billion and is projected to reach $36 billion by 2027, indicating a good compound annual growth rate (CAGR).
Key Drivers of Growth:
- E-commerce: The rise of e-commerce platforms has increased the demand for efficient cold chain solutions to deliver perishable goods safely and in a timely manner.
- Pharmaceutical Needs: Due to the low cost of manufacturing, and government subsidies, India is the third largest manufacturer of medicines in the world. The pharmaceutical industry requires stringent temperature control to transport products like vaccines and other sensitive items.
- Agricultural Produce: India's substantial production of fruits and vegetables requires effective cold storage and transportation to minimize post-harvest losses.
While the opportunity exists, businesses must adopt practical solutions to optimize their cold chain logistics. This article explores the current landscape of cold chain logistics in the country, common challenges, as well as best practices that leverage technology and management techniques to ensure efficiency and reliability.
Common Challenges
Cold chain logistics faces several challenges, particularly in maintaining temperatures throughout the supply chain. These challenges are the result of:
- Temperature Fluctuations: External factors such as weather changes, power outages, or inadequate refrigeration units often lead to temperature fluctuations. Even minor changes can compromise product quality, especially for sensitive goods like vaccines and dairy.
- Fragmented Infrastructure: Over 90% of India's cold chain sector is fragmented and privately owned, and therefore lacks standardization. This fragmentation leads to inefficiencies and quality inconsistencies among the various market players.
- Lack of Real-Time Monitoring: Traditional cold chain systems rely on manual temperature checks and delayed reporting. This delay in identifying temperature changes or crashes can result in irreversible damage to products, incurring great losses.
- Poor Infrastructure: Inadequate storage facilities, poorly maintained vehicles, and unreliable cooling systems can create bottlenecks in the cold chain process.
- High Operational Costs: Managing a cold chain is resource-intensive. Fuel costs for refrigerated trucks and energy expenses for storage facilities often strain budgets, making it harder for businesses to balance cost-effectiveness and quality.
- Regulatory Compliance: Stringent rules for temperature-sensitive goods demand rigorous documentation and adherence to standards. Non-compliance can lead to fines or damaged reputations (a big loss in this industry).
10 Best Practices in Cold Chain Logistics Management
Addressing these challenges requires a blend of operational best practices and advanced technologies. Here are some tried and tested solutions to optimize temperature management in cold chain logistics:
1. Standard Operating Procedures (SOPs)
Develop and enforce detailed SOPs for handling, storage, and transportation of temperature-sensitive goods. Ensure that these procedures are regularly reviewed and updated based on operational insights and regulatory changes.
2. Adopt AI-Driven Analytics
AI-powered platforms like those offered by Fleetx can analyze historical operational data to predict potential risks in the cold chain. For example, AI can identify patterns in equipment performance and forecast maintenance needs, reducing unexpected breakdowns. Additionally, AI tools can optimize delivery routes, ensuring minimal transit times and reduced exposure to external temperature variations.
3. Pre-Cooling Products
Ensure that products are pre-cooled to their required storage temperature to minimize the strain on cooling systems during transit. This helps maintain temperature consistency.
4. Temperature Validation
Perform regular temperature mapping and validation of storage facilities and vehicles. This ensures that all cooling equipment meets the necessary temperature requirements. Different products have specific cold chain requirements (e.g., frozen vs. chilled goods). Tailor your systems and processes to meet these specific needs for optimal results.
5. In-Transit Packaging
Use advanced insulated packaging materials and gel packs to maintain optimal temperatures during transit. Packaging solutions should be tailored to the specific product requirements.
6. Emergency Systems
Install backup refrigeration units and power supplies in storage facilities and vehicles. This ensures operations can continue seamlessly during equipment failures or power outages. Develop contingency plans for handling disruptions, such as equipment failure, vehicle breakdowns, or extreme weather events. Train staff to implement these plans efficiently.
7. Regular Audits
Conduct internal and external audits to assess compliance with cold chain standards and identify areas for improvement. Leverage vehicle telematics solutions, where possible, to automate the process. Proactively mitigate risk to ensure fewer surprises in the future.
8. Strategic Partnerships
Work closely with logistics partners to ensure they adhere to your cold chain standards. Sharing data and aligning on temperature management expectations can lead to smoother operations and prevent disruptions.
9. Ensure End-to-End Visibility
Integrating temperature monitoring systems with GPS-enabled tracking provides end-to-end visibility into cold chain logistics. Fleet managers can monitor vehicle locations and conditions in real-time, ensuring that goods remain within the required temperature range from origin to destination.
10. Continuous Staff Training
Provide regular training sessions for staff to familiarize them with the latest technologies, equipment handling, and compliance standards. Well-trained personnel are critical for maintaining a reliable cold chain system.
Including these practices in your operations will improve your operational efficiency, as well as offer additional layers of protection against the various risks involved.
To Wrap Up
The future of cold chain logistics looks bright, with trends showcasing enhanced supply chain visibility, integration of advanced technologies, and a shift toward sustainable practices. Furthermore, government initiatives like the National Center for Cold-chain Development (NCCD), and events like the All India Cold Chain Seminar and Exhibition provide a platform for industry players to collaborate and innovate, further driving the sector's growth.
In conclusion, while the cold chain logistics industry in India is on a promising growth trajectory, addressing infrastructural gaps, and embracing technological advancements are crucial steps towards realizing its full potential.
Fleetx’s advanced logistics solutions are designed to address these challenges, offering real-time monitoring, predictive analytics, and streamlined operations. As India’s logistics landscape evolves, adopting such innovative practices will be critical in meeting the demands of a growing market while minimizing waste and operational costs.