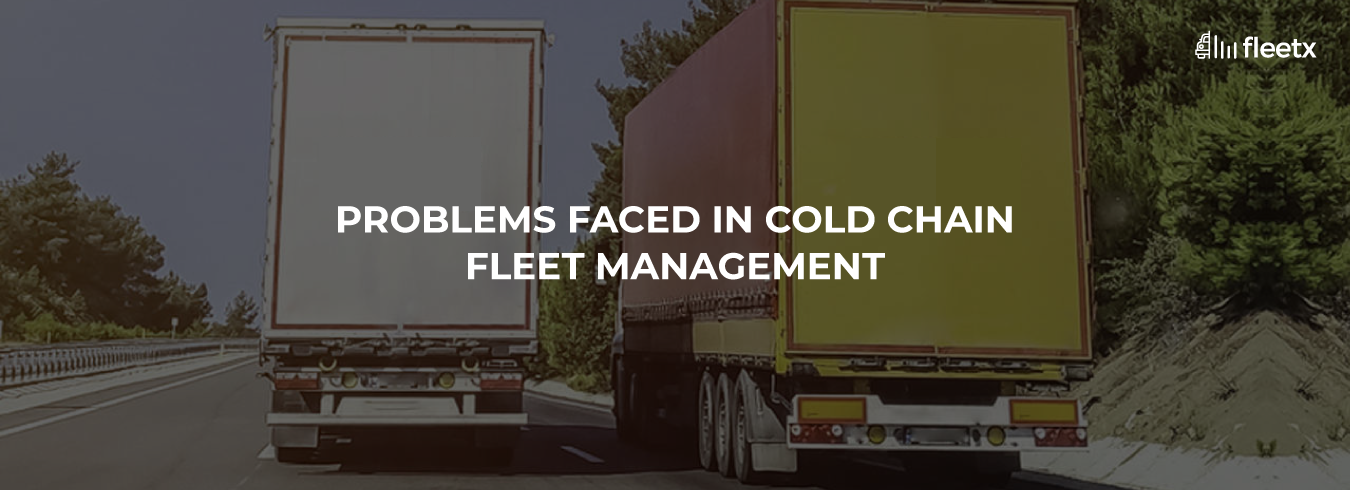
Cold Chain logistics is an incredibly crucial form of transportation of goods in this day and age. Especially now as COVID Vaccines are about to begin distribution, the responsibility of safely transporting them while making sure they don’t degrade due to uneven temperatures lies heavily on the shoulders of perfectly executed cold chain management.
As important as Cold Chain Fleet Management is, there are a lot of factors that make its execution a really difficult task. Shipments can get damaged during transportation and sometimes even before they reach their designated vehicle for moving. It is important to know issues beforehand which can help you prevent losses worth billions of dollars, and here are the 7 biggest problems that you need to know.
- LACK OF UNIFORM STRUCTURE
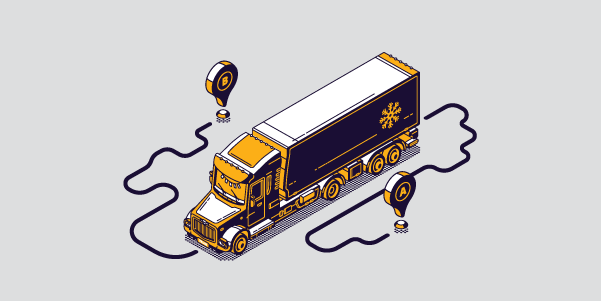
Though science has progressed leaps and bounds which has led to a great deal of stability in cold chain fleet management, we still are far from the optimum scientific stability and infrastructure required. For Example, even the most energy-efficient and advanced cooling system would not work without a power port to plug it in, that is if you have the right adapter and voltage, to begin with.
2. UNHYGIENIC MICROBIAL GROWTH
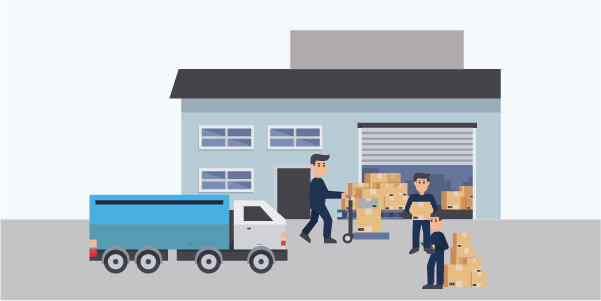
The growth of mold and mildew is yet another problem that plagues freezers. Mismanaged Temperatures or broken freezer doors can create .This issue, but can be managed easily by properly Monitoring your cold storage, the freezer walls themselves will minimize the microbial harborage and build up.
3. EXPOSURE DURING LOADING & UNLOADING.
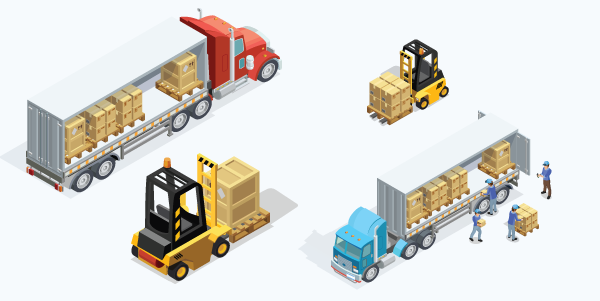
The handling of temperature-sensitive perishables can face problems before they even enter the cold storage. This is usually caused due to prolonged exposure to warm outside temperatures during loading and unloading, which severely degrade the perishables be it food, beverages or pharmaceuticals.
4. PACKAGING FAILURE
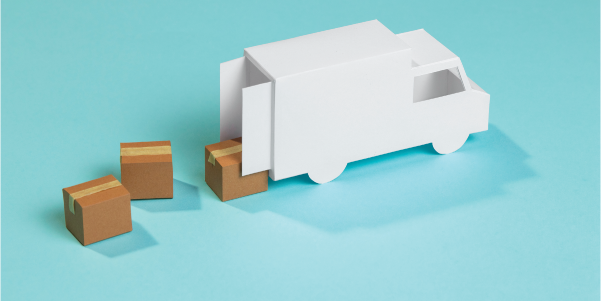
Maintained temperatures along with the proper packaging is important for perishable goods, and if the packaging Is not done correctly or is damaged it can cause the goods to degrade. It is essential to keep a check on proper Packaging and if there is any damage to it.
5. VEHICLE BREAKDOWN
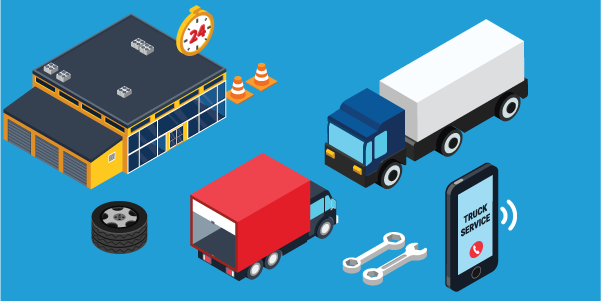
Vehicle breakdown can cause delayed shipments, and in the case of cold chain management, a delayed shipment can also be a destroyed shipment. This makes it really important to have constant tracking of your fleet so you can act quickly in such cases.
6. HARDWARE BREAKDOWN
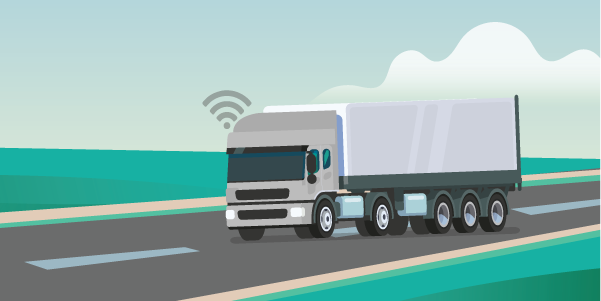
Hardware failures are common occurrences In cold chain fleet management, This could Include things like refrigeration equipment failing due to malfunctions, damaged Freezer doors, malfunctions of temperature sensors connected with GPS or simply loosing power supply.
7. TEMPERATURE FLUCTUATIONS
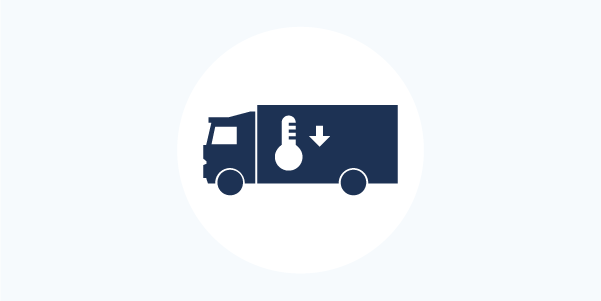
Temperature variances must be checked at all times, else the quality and safety of perishables can be severely impacted. Constantly opening the door exposes perishables to ambient temperatures which may be much higher than the temperature inside.
LET’S BE MORE PREPARED
Generally, if you have your Freezing units constantly monitored & have regular maintenance you would not have to worry about most of the problems. We hope that this article helped you broaden your horizons, and can help you manage your Cold Chain fleet much better. The world moves on logistics and fleetx will always help and make sure that your logistics move smoothly and efficiently.